Revolutionizing Clinical Supply Chain Management for a Global Pharmaceutical Company
By Boston Insights | Feb 21 2024
<span data-buffer="">Context<span data-metadata="">
Our case study revolves around one of the top global pharmaceutical companies, renowned for its robust drug pipeline and rapidly expanding product portfolio. Over the past few years, the company has made multiple major acquisitions and currently boasts a clinical trial portfolio of over 300 active trials sponsored by its research and development (R&D) department. With several new product launches the company’s rapid growth has placed significant stress on its Clinical Supply Chain Group.
<span data-buffer="">Challenges Faced by the Company:<span data-buffer="">
3. High Levels of Material Waste: The company faced a significant challenge in managing material waste, particularly with investigational medicinal products (IMPs) and comparators. Approximately 50% or more of these materials were being wasted, resulting in substantial financial losses.
5. Slow and Time-Consuming Planning Processes: The planning processes within the clinical supply chain were slow and time-consuming, leading to delays in study initiation and execution. This impacted the overall productivity of planners and the speed of clinical trials.
<span data-buffer="">Solution:<span data-buffer="">
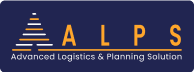
<span data-buffer="">ALPS - A Clinical Supply Chain Control Tower<span data-buffer="">
After careful evaluation of various options, including commercial off-the-shelf (COTS) control tower and analytics platforms, the company decided to implement ALPS – A Clinical Supply Chain Control Tower.
<span data-buffer="">How ALPS Helped Solve the Problems:<span data-buffer="">
<span data-buffer="">Conclusion<span data-buffer="">
Implementation of ALPS helped the company to improve their end-to-end visibility, enabled proactive risk management, material waste tracking, improved agility, enhanced collaboration, and reduced supply lead times. This resulted in a more efficient and resilient clinical supply chain, supporting the growth of its R&D pipeline, and ensuring the uninterrupted supply of critical medications to patients enrolled in clinical trials worldwide.